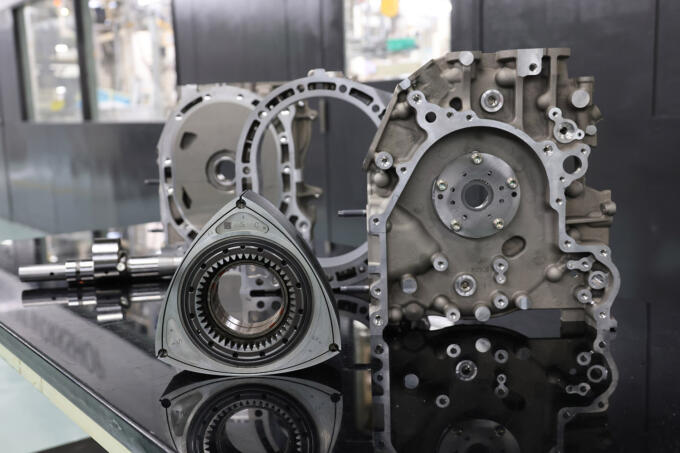
この記事をまとめると
■復活したロータリーエンジンも組み立てられている広島市のマツダ宇品工場を見学
■多くの場面で緻密な作業が可能なロボットが導入され11年前に比べてローターの精度が大幅に向上
■ロボットが導入されても「匠」と呼ばれるベテランの知識と経験がないとロータリーは完成しない
11年量産されていなくとも確実に進化していたロータリーの生産
ロータリーエンジンの生産は、2012年6月に生産終了となった「RX-8」の「13Bレネシス」でいったん途絶えてからは、補修用エンジンがごく少数生産されるにとどまっていた。本格的な量産は約11年ぶりのこととなる。
その新たに「8C-PH」と名付けられた発電専用のロータリーエンジンと、それを搭載する「MX-30 e-SKYACTIV R-EV」が生産される、広島市のマツダ宇品工場を見学する機会に恵まれた。
8C-PHはすべて内製で生産される。今回見学したのは、エンジンパーツの生産および組み立てと車体の組み立てのラインだ。ロータリーエンジンの生産ラインは、以前、13Bレネシスを生産していたラインを8C-PHに合わせて変更したものだ。
8C-PHは、EVモデルと同じ車体に搭載するため、2ローターではなく1ローターとされ、ローターの大型化が図られたのが大きな特徴だ。それもあって、これまでにも増して高い精度が求められることになった。
まず、ローターの大型化により、回転時のバランス変動において不利になることに対して、ローターのバランス精度の向上が必要となる。また、燃焼の改善や排気量の拡大により燃焼圧力が高まることから、シール精度の向上が求められる。
ローターを砂型で鋳造する際に、これまでは中子と呼ぶものを挟み込んでいた。すると、中子の精度が非常に重要となる。どうしても限界があったところを、マシニングセンターを用いて精巧に加工する手法を採用した。
また、加工ラインについて13B時代には切削に50工程を擁していたところ、工程の集約により、9工程にまで大幅に削減することができた。生産時には多くの工程でロボットアームがマシン間でローターを掴み換えるのだが、工程の削減により掴み換えが最小限になったことも、精度の改善に寄与している。